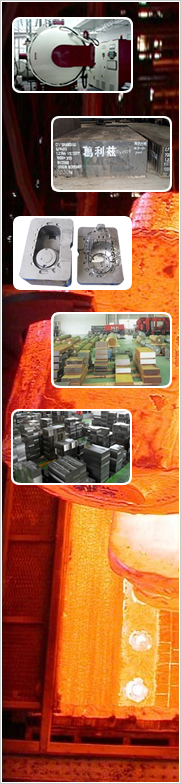
The reason for the die early cracking
- 1)When the mould is in die casting processing ,the mold discharging agent sprayed unreasonably.
- 2)the mold heat treatment is not ideality, the key is hardness . (hardness shall be not less than HRC--47).
- 3)The quality of the steel mold is not good, suggesting to use the special refining material H13ESR-SUP.
- In general, the reason for early cracking is the rough forging temperature starting too high(usually said overburning) the overburning is an irredeemable defects,so we should strictly control the forging temperature in the blank processing period .So does the quenching technology,to strictly control the heat time to avoid decarbonization.After choosen the material,it is heat treatment .And we should pay attention to the stress after producing a certain number of products . In addition ,the design should be reasonable , to try to avoid stress concentration and note that the control of the size for R angle .When the die using life is 10000 times ,we should noted that the stress tempering .All in all ,the crack is the expression for the stress concentration .we can adopt many times tempering to dislodge the stress ,accordingly to increase the die life .
- The reason of aluminum alloy die-casting mold will crack in production after a period of time, mainly has following several points:
- (1)Mold temperature is very high and the stress is too large.
- (2)Mould material use H13ESR-SUP/2344ESR
- (3)The hardness of mould heat treatment is too high
- (4)Regular maintenance,5k times for first tempering ,15k times for second tempering ,30k times for third tempering ....
- ..To prevent of die cracking problem and to improve the service life of the die, we must do the following:﹕
- 1.Die casting molding parts( mold ,core )heat treatment requirement ,hardness should be ensure in HRC43~48( material can elect H13ESR-SUP/2344ESR)
- 2.Before the mould produce ,it should be full preheated, its role is as follows:﹕
- 2.1To achieve the heat balance better and to make casting solidification velocity and to be conducive to the pressure transfer.
- 2.2To keep the liquidity in the die casting alloy filler ,to have good molding properties and improve the casting surface quality ..
- 2.3To reduce the bad quality before production ,improve the casting production rate.
- 2.4To reduce the mould heat alternating thermal stress ,improve the die life ,detail standard as bellow :﹕
alloy type
|
alluminum allo
|
zinc alloy
|
mould preheat temperature(℃)
|
180~300
|
150~200
|
- 3.After produciton a period of time for the new mould, the accumulation of the thermal stress is directly reason to cause cracks.In order to reduce the thermal stress, we should do the tempering treatment for the mold and slider after putting into production a certain period time .The specific way to eliminate thermal stress which is corresponding to the production mode time as follows:
mould type
|
first time tempering
|
second time tempering
|
the third time tempering
|
aluminum alloy
|
<2000 using times
|
<10000 using times
|
<30000 using times
|
zinc alloy
|
<10000 using times
|
<20000 using times
|
<50000 using times
|
- Aluminum alloy die-casting bears a great alternating work stress. It must be noted that the mold material, design, machining, heat treatment and operation ,about all the aspects ,to keep the long time die life .There are are 22 tips to keep the die life as long time as possible :
- 1、High quality material
- 2、Reasonable design for the mould wall thinkness and the other mould size
- 3、Try to adopt the casting insert
- 4、Selection of angle R as large as possible in the possible conditions
- 5、The Space of the coolant gallery and moulding surface and angle must be large enough
- 6、After rough machining ,it should be to stress tempering
- 7、The correct heat treatment, quenching cooling must be fast enough
- 8、Thorough grinding to remove EDM bad quality layer
- 9、The moulding surface should not be highly polished
- 10、The moulding surface should be oxidation
- 11、If choose nitriding, carbonitriding layer should not be too deep
- 12、According to the right way to preheating the mould to the recommended temperature
- 13、Beganning to die 5 ~ 10 pcs mould ,it should be used the hammer speed
- 14、On the premise of getting the qualified products , it should reduce the temperature of aluminum liquid as far as possible.
- 15、Do not use high injection speed for the aluminum liquid .
- 16、To ensure the mold properly cooling, cooling water temperature should be maintained at 40~50 ℃
- 17、The machine is temporary shutdown, it should try to mold and reduce cooling water, to avoid the mould under thermal shock when restart the machine.
- 18、When the model surface at the highest temperature ,it should be closed cooling liquid.
- 19、Don’t spray the mold discharging agent too much .
- 20、After a certain number of die casting ,it should be done stress tempering
- 1、The main reason is temperature is too high ,we suggest to use the thermometal to control it when in die casting .(aluminum alloy die casting temperature should be less than 650 degree)
- 2、Noted the preheat for the mould ,to avoid the thermal fatigue (crack mainly caused by thermal fatigue )
- 3、Noted the processing for the mould ,it is best to finish at the machining center,if it should do the Electrical discharge machining, After EDM ,it should increase the grind and polish work ,
- 4、Noted the maintenance for the mould (stress tempering )
- 5、For the high life requirement ,we suggest to use the material H13ESR-SUP ,the hardness for the casting die should not be higher than 51HRC ,About this way and experience ,you can use for reference ,except the zinc alloy casting die and other special demand .